Ecofilter
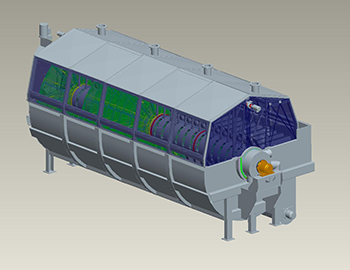
Continuous disk-type rotary filter.
The tank functions as a container. The filter itself, the mechanism which allow it to function, the central shaft and disks are all found inside the tank which is made of welded stainless steel sheets.
The power supply apparatus is welded to the tank for its entire length.
The entry plugs are positioned at an equal distance between them.
The apparatus id made upon a number of disks mounted on a central shaft cable every disk os composed of 18 sectors on whose the filter screen is mounted.
Each sector of the disks is firmly bound to the shaft by means of radial rods.
This allows for an easy removal of the part. The size of the filter will therefore depend upon the number of disks used as well as the amounts of the water to be treated.
The central shaft is made of welded stainless steel sheets and has a number of longitudinal compartments equal to the number of sector of the disk.
One end of the shaft is closed while a distributer valve is mounted on the opposite end.
The distributer valve is mounted on the opposite side of the principle commands.
The contact surfaces are made of a material which is almost friction-free.
The valve has two functions: the first is to separate the filtered wasters into three parts in terms of their quality, determined by the quantity of suspended solids present.
The second function is to create a system of communication for each of these waters whereas they will be made to flow into barometric vertical tubes that, in turn will create a vacuum necessary for their filtration.
In effect, water passes through the filter support of the sectors of the disks; during its rotation, however it will initially have a minor capacity of retaining impurities.
The valve thereby conveys this first fraction towards the sorted torbid waters by means of a canal that will, in turn, send the waters back to the head of the system.
As the rotating action of the filtrating support continues, the layer of the retained impurities thickens, constituting a filtrating surface that will thus allow for a further filtration of minute particulate.
On their way out, the waters are therefore clearer and the valve will provide to the canalization of these waters towards another area for stockage.
The filter is equipped with a regulating device that will allow variations in rapport for the three rangers in function with the position of the slurry wall that distinguishes the passage of the waters in exit through the valve.
Due to its structure, the valve connects the vacuum to the sectors relative to the discs that will be plunged and it is maintained until the sectors relative to the discs that will be plunged and it is maintained until the sectors come in proximity with the nozzles situated in the higher part of the filter.
The filtration process therefore initiates with the immersion of the sectors in water and terminates with their coming afloat.
The layer of waste is removed by means of a jet of water and is discharged through a drainage slide that, in turn, conveys the accumulated matter unto a millhopper which is situated in the lower external part of the tank.
From here, by means of a screw nut, the collected matter is conveyed for the recuperation of the fibres ( for the paper mill industry) and to a filter press (for marble quarries) in order to obtain a complete dehydration.
The filter is equipped with two series of nozzles: the first series is utilized for the drainage of the accumulated matter that is deposited and recuperated from the filter screens.
The second series is for the appropriate washing-cleaning and is finalized in obtaining clean sectors when the immersion takes place.
The water used for the cleaning of the sectors that remains in the main shaft will be separated by the same valve and will, by gravity present in the valve, then be conveyed unto the drainage cavity-hole.
The water is then sent back to the head of the system.
The movement of the shaft that carries the disks is assured by a group of twin-motor gearboxes with variable velocities.
The water is then sent back to the head of the system.
The movement of the shaft that carries the disks is assured by a group of twin-motor gear boxes can be piloted in terms of velocity.
When the flow leading to the filter, augmenting the level in the tank, the device increases the velocity if the rotations, and also, therefore, the amount passing through the disks in time units.
Vice versa, when the flow decreases, diminishing the level in the tank, the controller diminishes the velocity.